UdeC’s Faculty of Engineering has made progress in producing copper foil, a key component for electronic devices, from cell phones to electric vehicle batteries. This is being manufactured via a new method using unconventional solutions generated in the mining-metallurgical industry.
By: Carolina Vega Artigues, Journalist – Faculty of Engineering cvegaa@udec.cl | Images: Courtesy of the Faculty of Engineering
Innovating, reducing costs, and minimizing environmental impact are part of the objectives of a group of researchers from the University of Concepción, led by Dr. Eugenia Araneda Hernández, in alliance with the company Atacama Copper Foils. The novelty is that they have moved towards producing copper foil, a key component for electronic devices.
“Today, the large copper mining industry in Chile is focused on two products: a copper concentrate, or, a little higher in scale, grade A copper cathodes. That said, the idea behind the project is to pivot the industry by introducing this high-value copper foil production method,” explained Dr. Araneda a few months ago when receiving funds from Startup Ciencia 2024 for this initiative.
This technology is being developed in the electrochemistry laboratory of UdeC’s Department of Metallurgical Engineering (DIMET), where a team of engineers led by Dr. Araneda is making progress in copper foil production, whose commercial level thickness varies from 10 to 107 microns.
The project is the result of an alliance between the company Atacama Copper Foils and UdeC, initiated in May 2022 when a development contract was signed to produce copper foil. According to Transparency Market Research (2017) estimates, this foil will have annual growth rates exceeding 8% and a market estimated at USD 17 billion/year, according to the Natural Resources Division of the Economic Commission for Latin America and the Caribbean (ECLAC).
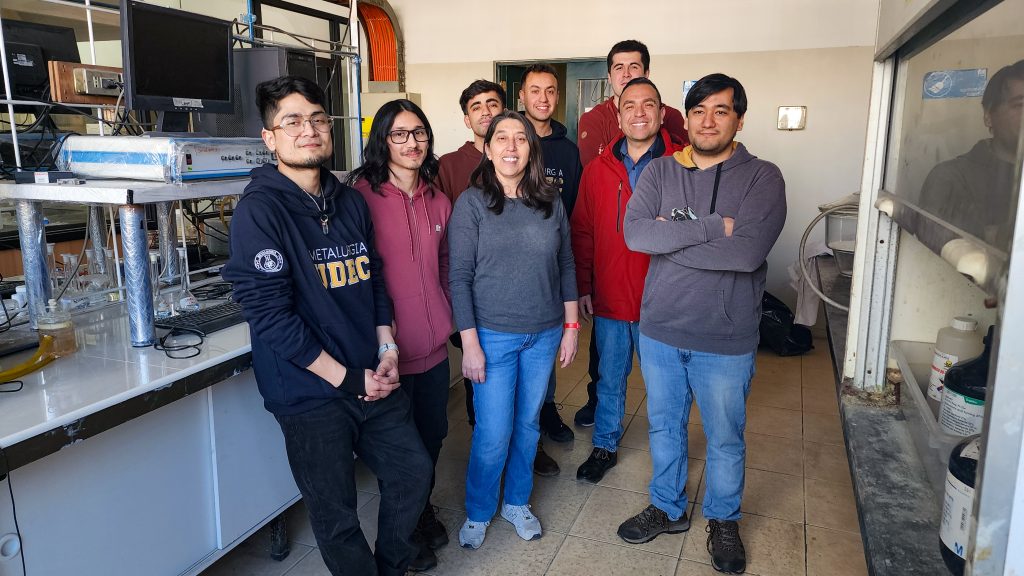
The idea and the development behind its manufacture have evolved into a patentable process that uses unconventional solutions generated in the mining-metallurgical industry instead of pure solutions, which is the traditional way. This reduces costs and the process’ carbon footprint.
Unlike the traditional copper cathode, which requires additional steps to reach a finished product, this is an end product. Although other countries have industrial-scale copper foil production, in this case, the method generates the product from a solution with low commercial value (discards or “poor electrolytes”). A growing demand for copper is also expected in the short term. According to the firm Maximize Market Research, it is estimated that, by 2030, almost 40% of the copper produced will be used as Cu foil.
“It has been a privilege to reach this stage working collaboratively and closely with entrepreneurs and investors. It makes us proud. We dreamed of seeing how a small idea became a real prototype, and now we are moving towards its industrial scaling,” said the DIMET professor.
Alongside Dr. Araneda, the research team comprises professors Froilán Vergara, Fernando Parada, and Roberto Parra, as well as young and motivated metallurgical engineers and a technical team. They add new value to contaminating products through their work, laying the foundations for more efficient, sustainable mining with an international projection.
Last modified: 23 de febrero de 2025